Injection molding is a common manufacturing process used to create plastic products with a high level of accuracy and precision. To produce large quantities of products, manufacturers use multi-cavity molds that contain several cavities or cavities arranged in a matrix pattern.
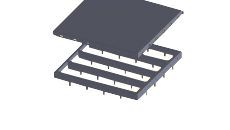
Designing a multi-cavity mold requires knowledge of the injection molding process, plastic behavior, and tool design. The process of designing a multi-cavity mold using SolidWorks software can be broken down into several stages.
Stage 1: Part Design
The first stage in designing a multi-cavity mold is to create a 3D model of the part that needs to be produced. The part design should include all the features required for the final product, such as undercuts, threads, and bosses.
The part design should also take into account the injection molding process. Designers should ensure that the part has uniform wall thickness, sufficient draft angles, and is free from internal stress.
Stage 2: Mold Layout
Once the part design is complete, the next stage is to create a mold layout. The mold layout is the arrangement of the cavities in the mold base.
Designers need to specify the number of cavities required for the production volume and the size of the mold base. The mold layout should also consider the ejection system, cooling system, and the gating system.
Stage 3: Core and Cavity Design
The core and cavity design involves creating a 3D model of the cores and cavities that will form the part. Core and cavity design requires expertise in mold design and plastic behavior.
The cavity design should consider the parting line, parting surface, and the runner system. The core design should consider the ejection system and the movement of the plastic material. Core and cavity design should also consider the shrinkage of the plastic material.
Stage 4: Mold Base Design
The mold base design involves creating a 3D model of the mold base that will hold the cores and cavities. The mold base design requires knowledge of mold design, assembly design, and machining practices.
The mold base design should include all the components required for the mold, such as the ejector system, cooling system, and the gating system. The mold base design should also consider the parting surface and the alignment of the cavities.
Stage 5: Assembly
The final stage is to assemble all the components of the mold into a complete unit. The assembly should consider the alignment, clearance, and interference of the components.
The assembly should also consider the ease of maintenance, disassembly, and repair of the mold. The assembly should be tested for fit, function, and accuracy.
In conclusion, designing a multi-cavity mold using SolidWorks software requires expertise in injection molding, plastic behavior, and mold design. The process involves several stages, including part design, mold layout, core and cavity design, mold base design, and assembly.
Designers should consider the final product design, production volume, injection molding process, and tool design in each stage of the process. With proper design and testing, multi-cavity molds can produce large quantities of high-quality plastic products.