Polyoxymethylene (POM) is a thermoplastic engineering material known for its excellent mechanical properties, such as high stiffness, low friction, and good dimensional stability. It is also easy to machine and has good resistance to wear and chemicals. Therefore, it is widely used in industries such as automotive, electronics, medical, and consumer goods. However, to fully leverage the benefits of POM, high precision molding is crucial. In this blog, we will discuss why high precision molding is important and how it can be achieved.
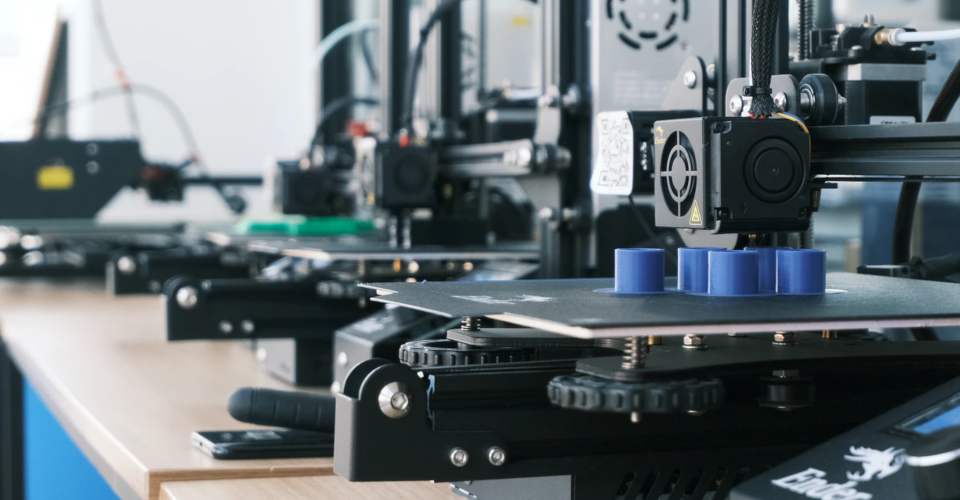
What is High Precision Molding?
Injection molding is a process of forming plastic parts by injecting molten material into a mold cavity, where it solidifies and takes the shape of the mold. The quality of the molded part depends on several factors, such as the design of the mold, the properties of the material, the process parameters, and the equipment used. High precision molding refers to a molding process that can produce parts with tight tolerances, consistent dimensions, and minimal defects. This requires a high level of control over the entire process, from material preparation to part ejection.
Why High Precision Molding is Important?
High precision molding is important for several reasons:
1. Quality: Precision parts require precise molding. Any variations or defects in the mold or process can affect the functional or aesthetic properties of the part. For example, in medical devices, precision parts are critical for patient safety and efficacy. In automotive parts, precision parts can improve performance, reduce noise, and increase durability.
2. Cost: Precision molding can reduce the cost of manufacturing by minimizing scrap, rework, and inspection. It can also increase the productivity of the molding process by reducing downtime, cycle time, and setup time. Moreover, precision parts can improve the assembly process by reducing the need for post-molding operations.
3. Innovation: Precision molding can enable the design and development of new products that require high accuracy and complexity. For example, microfluidic devices, optical lenses, and electronic connectors require precision molding to achieve the desired functionality and performance.
4. Sustainability: Precision molding can reduce the environmental impact of manufacturing by minimizing waste, energy consumption, and emissions. It can also improve the recyclability and reusability of the parts by reducing the need for secondary processing or assembly.
How to Achieve High Precision Molding?
Achieving high precision molding requires a systematic approach that involves the following steps:
1. Material Selection: Choosing the right material is critical for precision molding. POM is a good choice for high precision applications due to its low shrinkage, high strength, and stiffness. However, other factors such as the grade, the color, and the additives can affect the molding process and the part properties.
2. Mold Design: Designing a high precision mold requires careful consideration of the part geometry, the draft angles, the gating system, the cooling channels, and the ejection mechanism. The mold should also be made of high-quality materials and be properly maintained to prevent wear and tear.
3. Process Optimization: Optimizing the injection molding process involves adjusting the process parameters such as the temperature, the pressure, the injection speed, the holding time, and the cooling time. It also involves using advanced technologies such as injection velocity control, cavity pressure monitoring, and microprocessor-based control systems.
4. Quality Control: Quality control is essential for ensuring the consistency and reliability of the molded parts. It involves measuring and inspecting the parts against the specifications, using tools such as micrometers, gauges, and visual inspection systems. It also involves using statistical process control techniques to monitor the process performance and detect any variations or trends.
Conclusion:
High precision molding is crucial for achieving quality parts in POM and other engineering materials. It requires a systematic approach that involves material selection, mold design, process optimization, and quality control. By investing in high precision molding, manufacturers can improve the performance, efficiency, and sustainability of their products, while reducing the costs and risks of production. As a leading provider of injection molding services, 3D Hubs offers high precision molding in POM and other materials, using advanced technologies and quality assurance processes. Contact us today to learn more about our capabilities and how we can help you achieve your manufacturing goals.